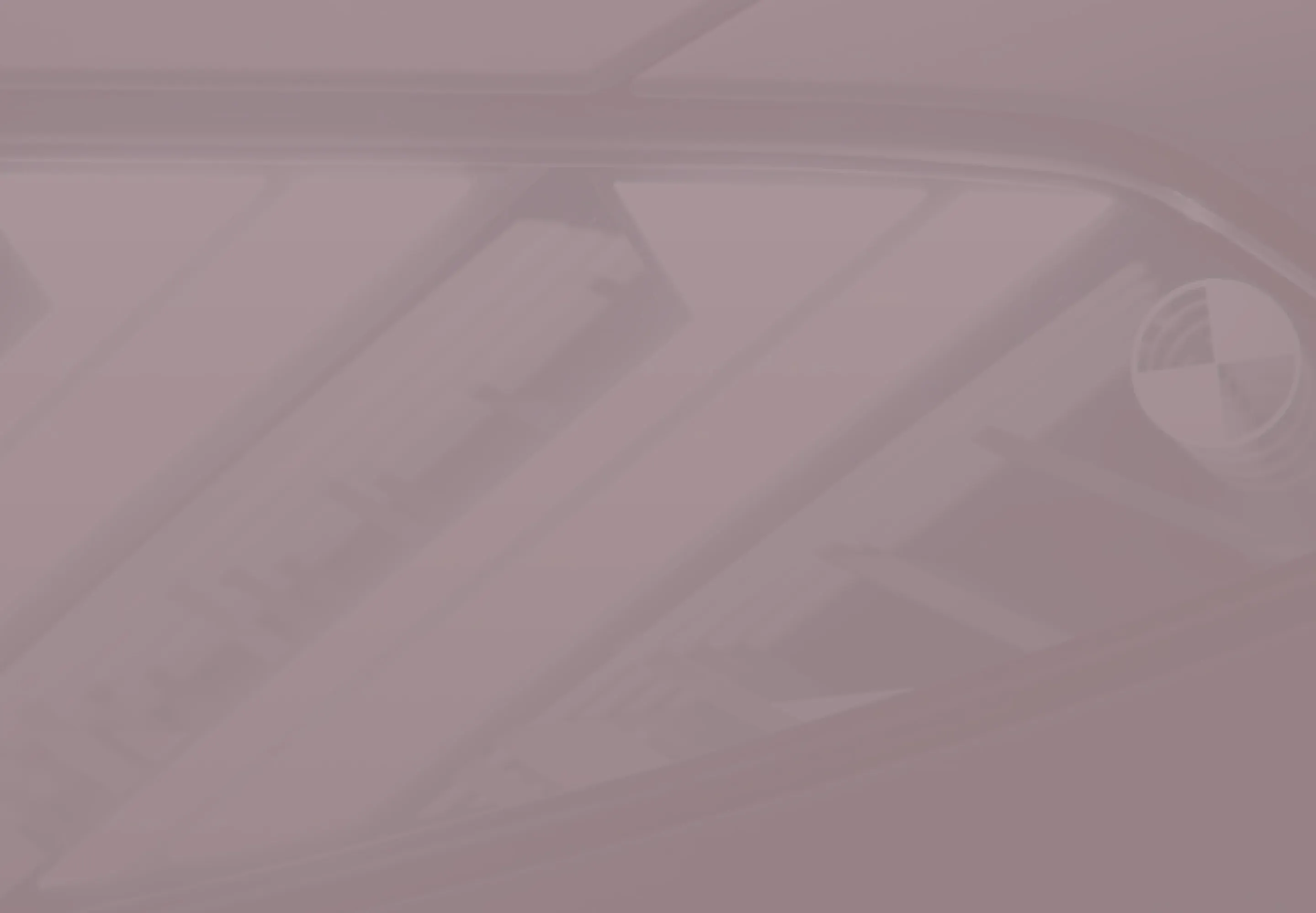
Enabling Location-based Process Automation: Our Investment in Kinexon
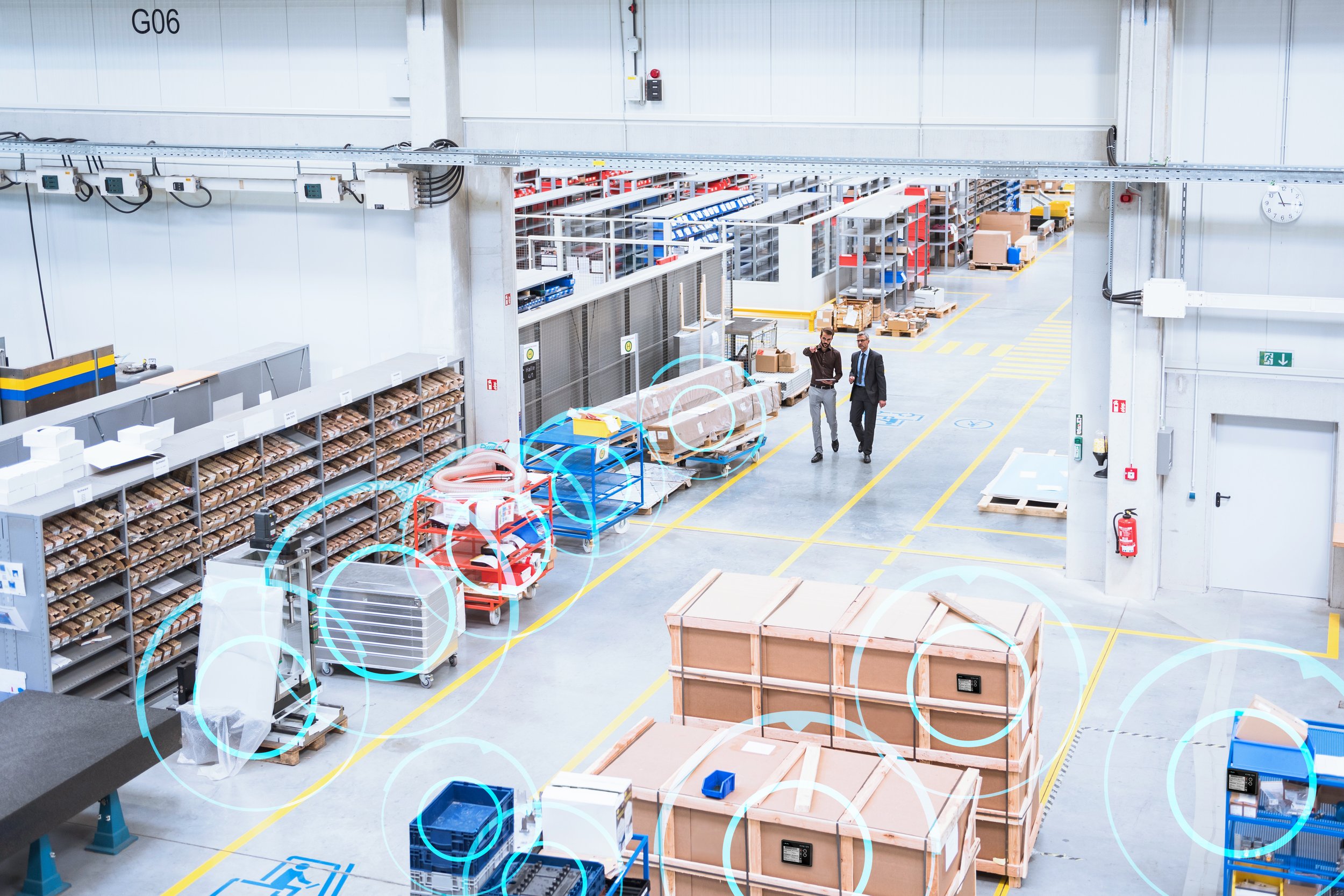
We are excited to announce our investment in Kinexon, a Munich-based technology leader for localization solutions based on its software and connected devices for the Internet of Things (IoT). Kinexon’s real-time IoT platform turns critical localization data for all moving parts on the shop floor into actionable insights, enabling the next generation of industrial automation for factory operators. Our investment in the company reflects the increasing industry-wide demand for smart production technologies that increase productivity and enhance workflows to enable the full vision of Industry 4.0.
Modern production facilities need to orchestrate thousands of moving assets at any given point in time, such as tools, raw materials, machinery, forklifts, autonomous robots, etc. Traditionally, these hardware assets were not connected to the network infrastructure in the factories, which meant that factory operators could not get a full picture of the inner workings of their operations on the shop floor. In order to effectively drive process automation, this needed to change. Accordingly, making systematic use of high-precision location information and connecting all real-world objects into a digital twin model represents a fundamental paradigm shift that promises to tackle inefficiencies and maintain high quality output in a constantly changing environment.
Meet Kinexon, the Next-generation Real-time IoT Platform
Kinexon confronts the traditional challenges of asset localization in the factory with its scalable Real-time IoT Platform (Kinexon OS) and its proprietary, ultra-wideband (UWB) sensor technology. The interaction between the hardware and software is what creates a synchronized location network that accurately and stably tracks all assets in a production facility. This system is also designed to allow for flexible integration into a wide variety of other localization technologies such as GPS, RFID, and UWB.
By combining these state-of-the-art technologies, their platform becomes the pinnacle operating system for all moving parts in production and logistics. It breaks up data silos and enables the interoperability of various systems across the entire shop floor. In addition, the aggregation of collected data allows for advanced analytics and event triggers, which unlock autonomous operations and location-based process automation.
To collect accurate localization data and create a digital twin of the physical space, Kinexon attaches UWB sensors to the desired moving assets. The digital twin is used to gain detailed insights that not only allow for proactive process monitoring, but also identify weaknesses in processes via process mining. For example, the software intuitively visualizes complex object flows in heatmaps that can help identify and resolve bottlenecks or potential clashes on the shop floor.
Providing the right information at the right time is crucial to trigger events that enable workflow automation in a variety of processes on the shop floor. Ultimately, these event triggers result in meaningful and measurable business outcomes for the customer. On top of that, customers can benefit from additional microservices or leverage the no-code/ low-code approach to easily automate processes.
BMW and Kinexon’s longstanding working relationship
BMW and Kinexon already have a successful history of working together on the co-developed IPS-i platform. This is a key technology in BMW’s smart factories and makes Kinexon a valued partner of BMW’s production landscape worldwide.
IPS-i is an identification and localization platform that creates a real-time image of the plant by collecting the position data of moving objects in the production process. The solution allows BMW to precisely define the location of each car on the production line, in the parking lot, or in transit to the dealership. Apart from that, it also enables smart production capabilities such as tool detection and coordinated tool configuration/adjustment. The system, for example, can detect if a screwdriver is approaching the right part of the car, unlocks the tool if all parts match the customer’s configuration and sets the right parameters for the tool.
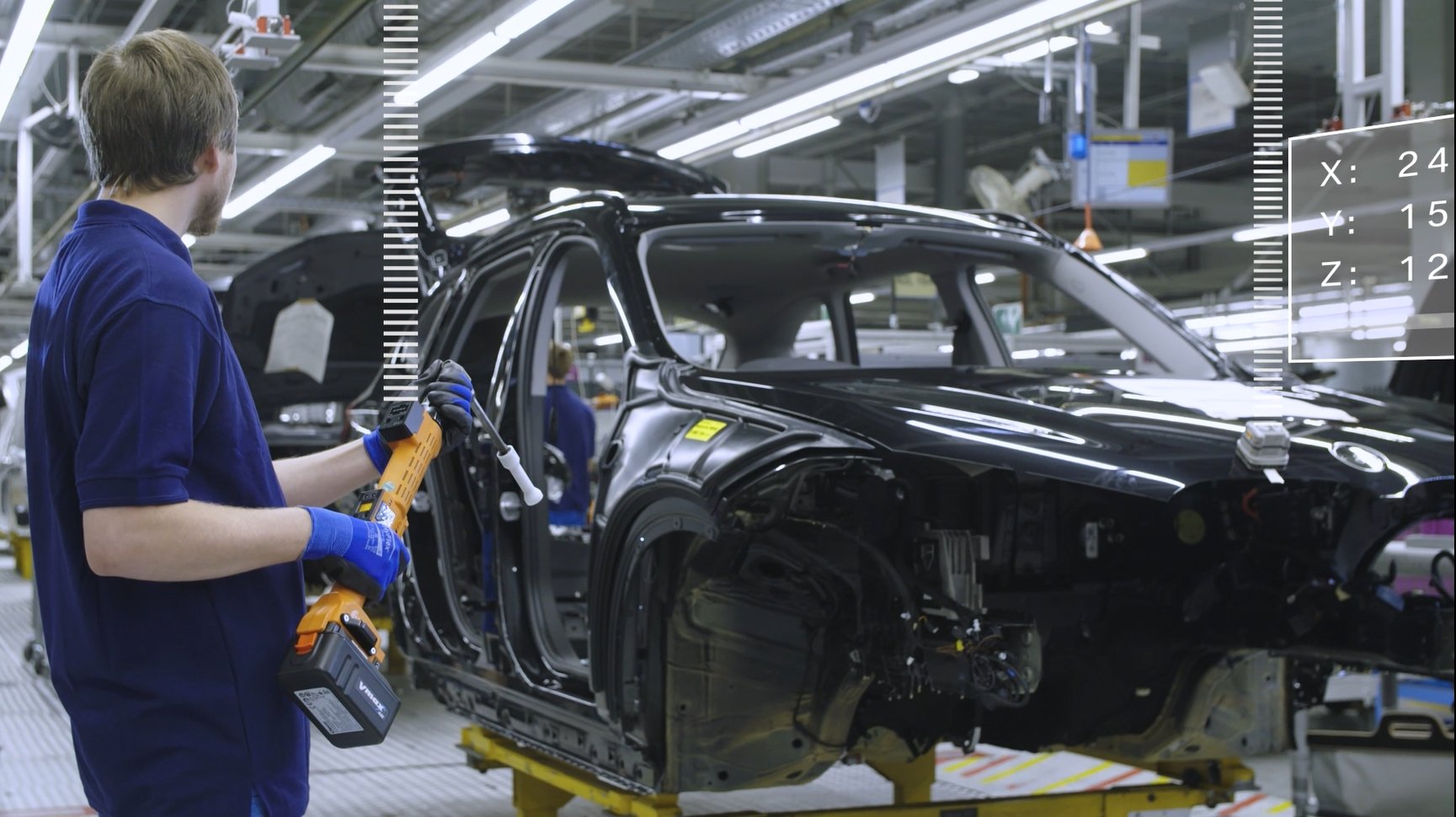
We believe that Kinexon is well-positioned to take a leading role in the connected and digitized shop floor of tomorrow and to set new industry standards for operational excellence, data insights, and real-time analytics. With this investment, we are thrilled to join and support Kinexon’s team as they embark on the next phase of growth, creating remarkable impact in the production landscape of the future.